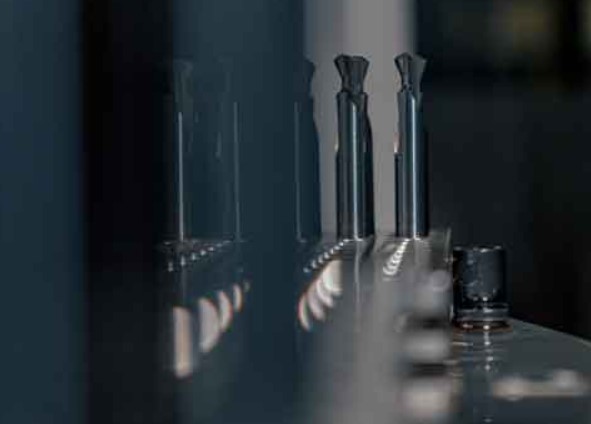
How to Create Custom Cutting Tools
Custom cutting tools offer a long list of benefits that most of you are probably unaware of. It’s because what was supposed to be an ordinary tool for cutting has been specially made into an ideal and personal cutting tool.
Thanks to this customization, you can work more efficiently. This high-efficiency level is made possible because of consistency, safety, and speed. Your custom cutting tool also gives you a better level of control, thus allowing you to produce minimal waste.
However, there are several areas that you should consider to make customizing your cutting tools easier and relatively more effective throughout your operations.

Table of Contents
Cutting Angle
The cutting angle of a cutting tool pertains to the angle where the cutting tool teeth’s upper face will engage the material cut. Also called the rake angle, this is the angle where the cutting tool’s tip enters and touches the material.
The various angles where the cutting tools and the material interact with each other determine the overall efficiency of the cutting. This cutting angle can range between -6 and 25 degrees and also determines the speed.
Before you customize your cutting tools, this is one aspect you should consider to condition them. You can opt for a 20 to 25 cutting angle if you expect a more aggressive cut from your custom tool. Meanwhile, a 10 to 15-degree customization may have a good speed rate although this one is lesser compared to 2o to 25.
A negative cutting angle is recommended for custom cutting tools for dense materials and metals. This is because you want a less aggressive bite from your custom cutting tool.
When customizing the cutting angle, you also do so while considering your power saw. You have to customize a negative cutting angle for the cutting tools that you plan to use with your radial arm saw. It will be quite dangerous to use a custom cutting tool with a positive cutting angle because of the difficulty involved with controlling the radial arm saw.
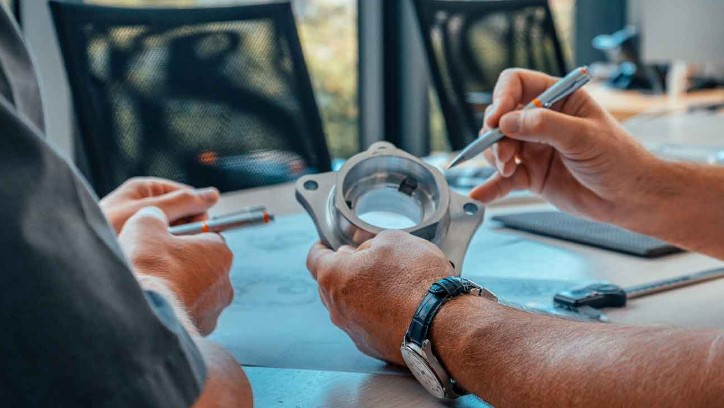
Cutting Material
It doesn’t matter if it is tile, asphalt, concrete, or wood, you must have your cutting tools customized based on the materials you plan to cut. It’s because every cutting tool comes with properties that give them adaptability in cutting through various materials.
Knowing the specific type of aggregate that makes up the material you plan to cut will allow you to customize the cutting tools and make them more appropriate for it. The Moh’s test is a common method you can use for detecting the aggregates. This test helps you determine the hardness of the aggregate, thus letting you customize the cutting tools based on it.
Determining the material you like to cut will also help you narrow down the cutting tools to specific properties and customize them based on these properties. The properties include the lifespan and cutting speed of your cutting tools.
If you only need to cut softer materials, your cutting tools can be customized to have a harder bond. However, if you will be cutting harder materials, you should customize your cutting tools to have a softer bond.
Material
Every cutting tool has a different composition, allowing it to cut through different materials. It is these variations that allow custom cutting tools to have certain properties unique to the particular materials they can cut.
The material composition of every cutting tool also has a certain purpose that allows them to work properly. When customizing cutting tools, you may add materials based on your desirable qualities, cutting tasks, and budget.
You can opt for custom brass cutting tools that are easy to make and fairly inexpensive but might be less durable. Metal cutting tools can be customized to provide flexibility because you can bend them to various shapes, are strong, and relatively cheap.
Customized metal cutting tools involve customizing from different varieties including aluminium oxide, vanadium steel, and stainless steel. In general, it comes with composite material coating. Customized abrasive metals are cutting tools with a material composition that lets them generate clean cuts and withstand heat.
You can also have custom diamond-cutting tools if you need better performance and strength. But take note that these can be expensive depending on the diamond crystal level you need. These custom diamond-cutting tools have a longer lifespan that eliminates the need for you to replace them more often. These custom tools made from diamonds can be continuous, segmented, or turbo.
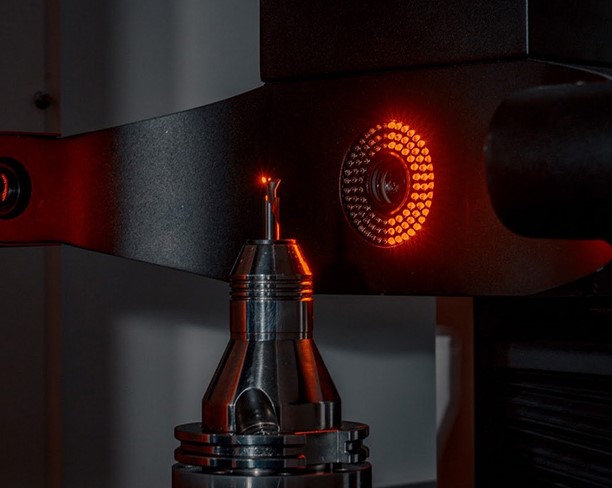
Number of Teeth
The number of teeth is yet another feature of custom cutting tools that will allow you to cut easily and correctly once you get everything right. It’s because this aspect has a significant effect on the overall cut. Cutting tools can have teeth ranging between 24 and 96.
This is why when customizing your cutting tools, you have to remember that the material you want to cut will be finer if your tool has more teeth. However, you need to compromise on looks to get the speed you need.
A cutting tool with a low number of teeth will allow it to cut fast yet rough. More teeth will create a fine finish but the cuts are slower. This is how things work: a cutting tool with few teeth has a bigger depth of gullet or spaces between the teeth. The tooth’s chipping action also has greater aggression, which means that every tooth can chip out a bigger quantity of the material.
But if the number of teeth is higher, the cut will be influenced by more teeth, thus letting every tooth cut only a tiny amount of the material. This means that when customizing your cutting tool, you should have a target number of teeth depending on the material you want to cut, the speed of the cut, and the smoothness of the cut. Having 24 to 40 teeth for your custom cutting tool means you prefer a rough finish but a fast cut. Meanwhile, 42 to 96 teeth can cut slowly but produce a smooth finish.
Always be wise when creating your custom cutting tools by considering the above aspects to get the best results.