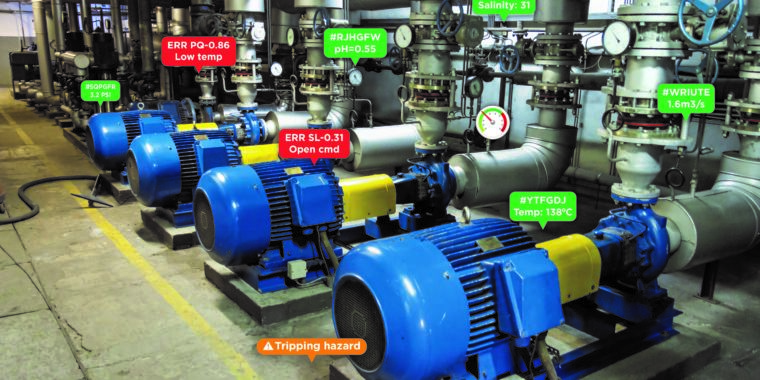
Augmented Reality is making industrial work more productive
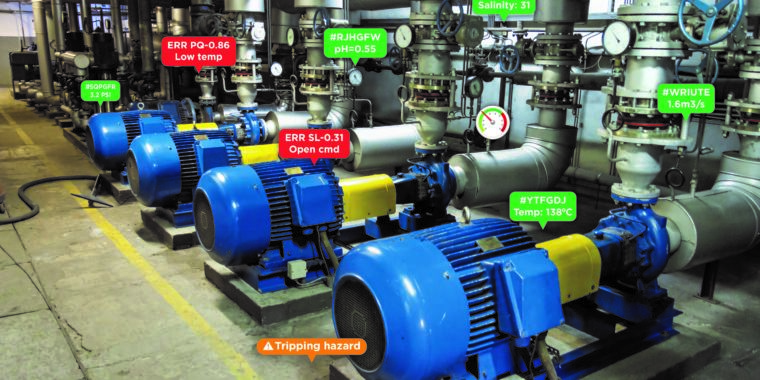
-
This is a screenshot of a Fieldbit AR view of a water treatment plant. The user can see equipment identification and telemetry tagged directly to individual machines.
-
Fieldbit isn’t a hardware company; their piece of the pie is in the software that provides the AR view. Workers don’t necessarily have to wear smart glasses; the Pokemon Go approach works too.
-
Another AR enhanced view of a treatment plant, this one from the outside. We’re not too sure the “tripping hazard” tags are useful when looking through your phone, to be honest.
Veolia Water Technologies, a transnational water treatment specialist firm, is partnering with a company called Fieldbit to bring Augmented Reality to the plant floor. Don’t feel bad if your first reaction to that statement is “huh?”—ours was, too. If you’ve ever had to work on unfamiliar or semi-familiar physical equipment, though, it gets pretty interesting.
We spoke to Robert Kodweis, Fieldbit’s VP of operations, to get a better picture of what the company really does. Fieldbit is a software company, and its apps are relatively hardware-agnostic. Users can experience AR (Augmented Reality) marked-up views of equipment and spaces through smartglasses such as Realwear’s HMT-1, or by using an Android smartphone app to mark up video from the phone’s camera in real time—something like Pokémon Go for the industrial floor.
-
In this shot, a lineman wearing the HMT-1 AR headgear has both hands free for climbing.
-
Realwear’s HMT-1 is IP66 water resistant—you wouldn’t want to take it SCUBA diving, but blasting it with your thumb over a garden hose is no problem.
-
This worker wearing a Realwear HMT-1 head-mounted AR computer inspects pressure and temperature gauges.
We pressed Kodweis pretty hard on the apparent AI aspects of the application. Since the press photos we saw mostly seemed to focus on tagging particular equipment with its own telemetry via AR, we wanted to know how the system was trained to reliably recognize individual machines without seeing identification plates and serial numbers. Kodweis explained that while this spatial computing is indeed possible, it’s not the big focus of Fieldbit’s collaboration with Veolia.
Instead, Fieldbit’s app provides remote workers with expert support in maintaining and repairing equipment on site. When a worker needs to perform an unfamiliar maintenance operation, he or she can open up the app and see if the operation is available in the company’s knowledge base. If so, the modern equivalent of Chilton or Haynes manual procedure outlines becomes available. If not, the field worker is connected with a remote support agent who can guide them directly through the procedure, seeing and marking up the camera images on the field worker’s device as they go.
-
A remote support engineer tags the video received from a field worker (left), and the markup appears on the worker’s tablet (right). This support session then becomes codified into a Knowledge Base entry, which later workers can access directly. The app will mark up their camera video automatically like the remote engineer did when creating the KB entry.
-
Some of us started out with Chilton manuals. These were great, but the line drawing diagrams were sometimes difficult to match up with real machinery in your hands or under your hood.
-
Haynes Manuals were usually an improvement over the older Chilton manuals, because they included real photos under the hood, with some anonymous mechanic’s hands on the parts in question.
-
Did you know there’s a Haynes manual for the Enterprise? There’s a Haynes manual for the Enterprise. How about that.
Fieldbit’s application sounds much better than a Haynes manual, though. Once a procedure has been worked up and added to the Knowledge Base, field workers can access it by first selecting the pump or other machine by model, and then selecting the procedure—which could be replacing a filter, replacing an assembly, or any general repair item. In the future, field techs will be able to just aim their phone or glasses directly at the machine and have relevant KB procedures pop up automatically—but the company is still working on the AI image recognition for that aspect.
Once the worker selects a repair or maintenance procedure, the Fieldbit app walks them through it step by step. At each step of the procedure, the app highlights the appropriate parts—for example, bolts which should be loosened can be circled in red—on the actual video of the machine, as seen on the field worker’s phone or headset in real time.
Listing image by Fieldbit