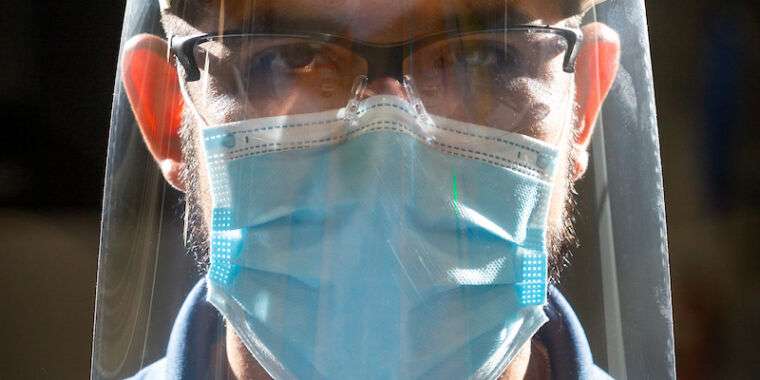
GM makes cars; how did it quickly pivot to face shields and ventilators?
Additive manufacturing and great logistics and supply chains all played a role. …
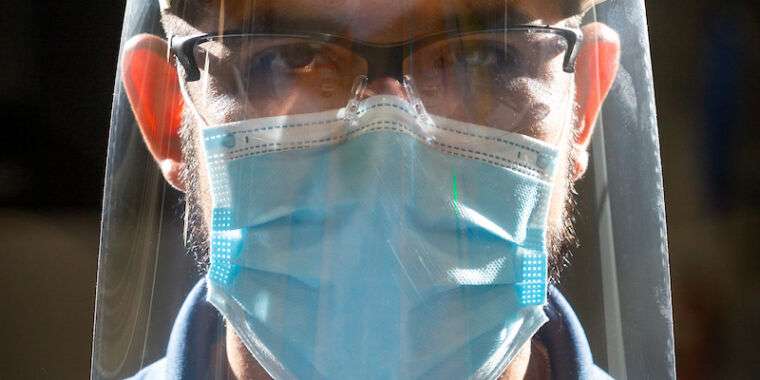
reader comments
49 with 36 posters participating, including story author
-
General Motors 3D-printed parts for more than 17,000 face shields that were donated to hospitals and first responders.
-
General Motors additive-manufacturing team members working at the still-under-construction Additive Innovation Center. The company uses a mix of printers from companies like Stratasys, Markforged, and HP.Jeffrey Sauger for General Motors
-
3D-printed ear savers help make masks more comfortable for some wearers.Jeffrey Sauger for General Motors
-
3D-printed fixtures (or nests) for ventilator production.Jeffrey Sauger for General Motors
The COVID-19 pandemic has changed the way many of us work, and that is certainly true for General Motors. The nation’s largest automaker might not be selling nearly as many cars as it hoped and has even pushed back some of its product releases (like a refreshed Bolt EV), but it’s been plenty busy. The company has switched gears and is using its resources and expertise to build ventilators and personal protective equipment like face shields to supply the healthcare sector. As it turns out, General Motors’ investment in additive manufacturing—3D printing to you and me—has played a big role in getting that effort up and running quickly.
View more stories
GM is no stranger to 3D printing, having first dipped a toe into the world of additive manufacturing back in the late 1980s. These days, as the technology has matured,
Continue reading – Article source