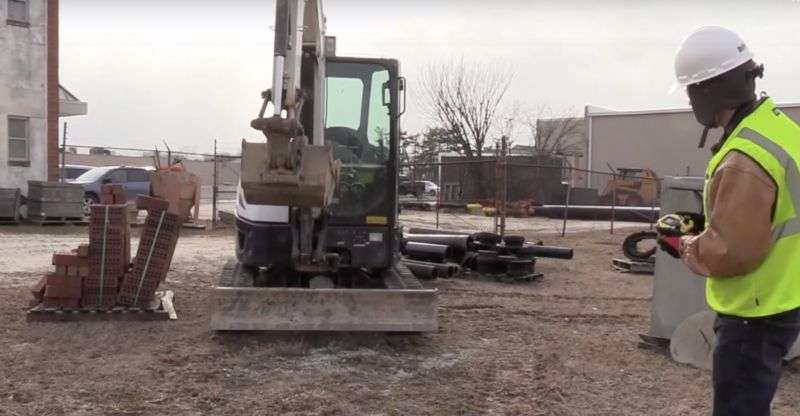
First-person digger: Stanley Black & Decker’s game controller for excavators
In a parking lot at an industrial and office park just outside Baltimore, I took a mid-sized excavator for a spin. I pushed around some cinder blocks with a leveling blade, nosed them around with the excavator’s shovel, and maneuvered the heavy metal beast around to make room for an incoming tractor-trailer. And I did all of this with a wireless controller that was almost identical to the one I used to play Forza the night before.
The excavator was configured with a prototype of the Remote Operated Control (ROC) System from Stanley Black & Decker’s Infrastructure Innovation unit—a bolt-on remote control system that allows heavy machinery from major manufacturers to be operated either from in the cab as usual or with a wireless game-style controller.
Stanley is currently recruiting contracting companies to act as beta testers for the technology, which is currently being targeted at Bobcat, CAT, Kubota, and John Deere excavators under 10 tons. The remote control kit can be installed in existing excavators in about 5 hours by someone with little to no mechanical experience. And the control system has a physical switch that allows an operator to quickly switch back and forth between local and remote control.
For now, ROC is intended for purely line-of-sight operations. But in the future, the technology could be used to allow remote operation of heavy machinery from nearly anywhere in the world. And with the addition of machine-learning technology, the same systems could eventually be used to automate some tasks or aid operators in doing them more safely.
There’s also another selling point for ROC: since its controller is so intuitive for people used to controllers for gaming consoles—I was able to pick up the basics in just a few minutes—it could be a way to expand the workforce. “Robot operator” might be a more attractive title for prospective employees than “heavy equipment operator.”
Heavy metal
Heavy construction equipment, much like other industrial technologies, is long-lived and rarely upgraded. “These systems are all hydraulics and have been around for over 30 years,” said Harry Zhong, technical lead at Infrastructure Innovation.
And because of the lifespan of heavy equipment, “the momentum required to shift the major [original equipment manufacturers] to fly-by-wire controls is huge,” he explained. “We know they’re going to get there, but in the meantime what we’re trying to do is create a digital bridge for legacy equipment.”
Stanley currently makes accessory tools for heavy machinery, including “breakers” (essentially large jack hammers for demolishing concrete), hydraulic shears, demolition grapples (giant claws), and other equipment that gets mounted on excavator booms for construction or demolition projects. Earlier this month, Stanley acquired the Paladin and Pengo business units of International Equipment Solutions, which make similar add-on equipment for construction, ranching, and agriculture. As a result, the company has a lot of experience working with the existing heavy equipment from the major manufacturers. And that could give Stanley a leg up in introducing remote operation to a wider range of customers.
ROC is not the first wireless controller on the market. But most of the existing remotes are “belly-pack” units built for very specific applications and are worn strapped to the body. These bulkier controls typically can only control the movement of the equipment’s boom from relatively short distances.
The ROC controller itself, developed by Humanistic Robotics, Inc., is based on work originally done for robotic landmine removal and improvised explosive device disposal. The ROC system currently uses a 900MHz UHF radio frequency for communications, allowing the controller to be used from up to a kilometer away from the equipment it controls.
-
The ROC controller is very similar to Xbox and Playstation game controllers—except for the big red button for emergency stop. Internally, it has sensors that can detect when it has been dropped. And all of the inputs can be programmed for specific tasks.
-
Inside the cab of an excavator, ROC actuators drive the same controls used by a human operator and allow a human to take over with the flip of a switch.
Tied to an onboard computer and actuators that work the existing controls in an excavator’s cab, the ROC controller allows operators to do a range of things they might not want to be in the cab for, such as using a shovel to assist an excavator in climbing a steep grade or operating a jack hammer on a small excavator lifted up by a crane for demolition tasks. At the same time, the controller allows the operator to get a better view when working over a ledge, or even act as his or her own spotter when using the arm as a light crane.
The game-style controller also allows for a wider range of functions, configurable for different modes of operation. On the excavator I got to drive, toggles in the position where triggers would be on an Xbox controller allowed independent operation of the machine’s treads. The controller also has a number of safety features, based on inertial sensors, that can detect when a controller is dropped, upside down, or idle. And a big red button can perform emergency stops; there’s also a separate safety supervisor controller that can perform the emergency stop function.
Inside the cab of the controlled excavator, the ROC control system uses control actuators tailored to each type of equipment, using existing bolts to lock them in place on hand controls and foot pedals. The actuators are tethered to ROC’s “brain,” a computerized control system in a ruggedized box (usually placed behind the seat in the equipment’s cab). The controller also monitors feedback from the controls over its own dedicated controller area network (CAN).
One of the main things lost with remote operation is what operators call “control feel”—the direct feedback from hydraulic systems during operation. While the loss of this inherent feedback from the hardware might not be a problem when the operator is right there next to the equipment, it could be a bigger issue when machinery is operated from a greater distance. Currently, the ROC system monitors system status and data and can detect issues like unexpected resistance of controls for added safety.
A fully machine-learning-driven excavator is a long way off. As issues with self-driving vehicle tests have demonstrated, even the most well-mapped environments can present problems that only a human can deal with. But there may well be a day soon when you can get “Bobcat as a Service” and have an excavator delivered and operated remotely by someone sitting in an office far away.